In November 2016 the Embassy of Sweden in Bangkok and Business Sweden brought a manufacturing delegation of Swedish companies to Thailand for the second year in a row.
This included, in connection to the Metalex Fair a seminar on the topic ‘Implementation of industry 4.0 in the Thai Manufacturing industry’, with the purpose to discuss the concept of Industry 4.0 and how it can benefit Thailand. In general Industry 4.0 refers to the fourth industrial revolution, where automation is combined with strong ICT capabilities. However, the seminar looked more closely specifically at digitalisation, sustainable production, competency and innovation.
In his remarks H.E. Ambassador Mr Staffan Herrström told how he had noted, during the year passed by since the last delegation, how various actors in Thai sectors – several ministries, private companies and institutes – have a common interest in Swedish solutions in the broad area of innovation, digitalisation and sustainable development. Sweden is happy to be able to facilitate that kind of interaction and co-operation.
“Thailand now wants to enhance their automotive and electronics manufacturing sectors, as well use as a basis to develop new industries from, and to elevate the country to a new level in industrial development. As a global manufacturing leader Thailand now has the opportunity to further develop the manufacturing industry in a sustainable way focused on innovation to meet the new sustainable development goals,” the ambassador also pointed out.
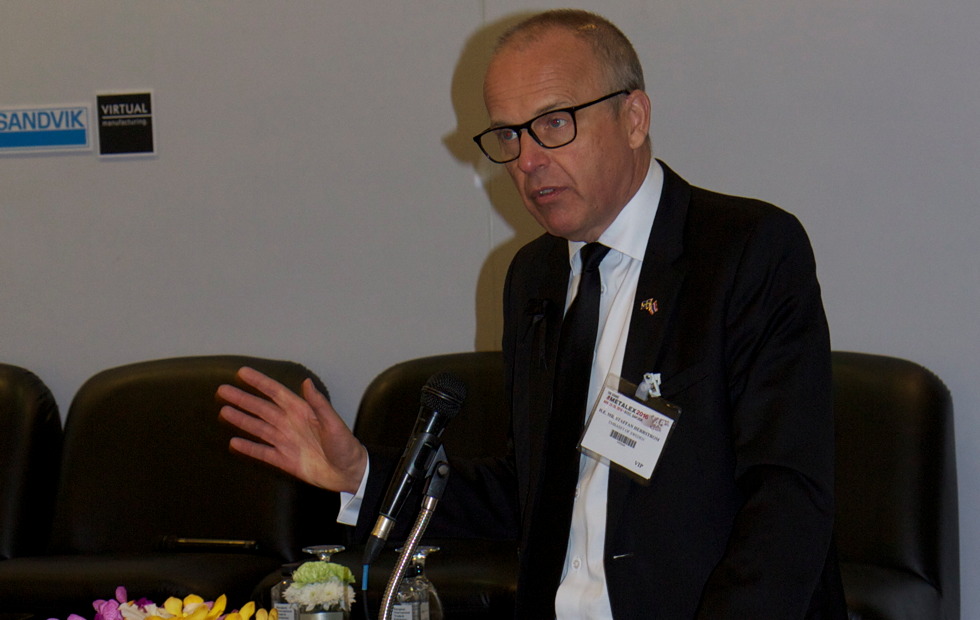
H.E. Ambassador Mr Staffan Herrström
“Definitely, the whole idea of changing to sustainable production patterns elevates our industries to a new level where knowledge is much more important than consuming resources. That’s part of the process of fulfilling those commitments and part of the process to reach the Industry 4.0.”
Dr Chayo Trangadisaikul, Deputy Secretary General for Federation of Thai Industries (FTI), in his presentation, talked about changes in Thai manufacturing industry, how coordination and Industry 4.0 in particular can support Thailand’s growth, and finally how to promote it.
Dr Chayo said that in comparing with the successful digitalisation of the retail sector manufacturing is different.
“Every manufacturing facility is different, unique in its way; in particular in Thailand where we did not start with a high level of coordination. We are relying in many cases on manual work, or semi-automation processing.”
Recently, FTI had conducted an industrial survey on Industry 4.0, categorising the level of industrial development into 2.0, 2.5, 3.0, 3.5, and 4.0.
“The result is stunning. For the 2.0 category, which involves manufacturing that employs electric power and some usage of conveyer system, we had 40 per cent of the respondents. So 40 per cent in this country is starting with 2.0. Then, in 2.5 – we define this as some use of mass production and with semi-automatic processes – 35 per cent of the respondents fall in this category. So we have the majority of manufacturing facilities in Thailand in 2.0-2.5, at 75 per cent!”
“To look on the brighter side we still have a lot of room for development and promotion of the Industry 4.0,” he continued. “We can lift those in 2.0, 2.5 into 3 – 3.5 and we are sure now that the manufactures already feel the heat of global and regional competition. And with the lack of labour in Thailand in terms of quantity and quality aspect of labour as well, now the requirement for the manufacturing is to do it cheaper, faster and more efficient. Automation then is the answer, and this is the point moving forward.”
The Doctor added that employees should not feel much concern regarding automation as replacement for human work, since Thailand experiences shortage of labour to begin with.
“On the other hand we feel very positive about retraining people, so they can feel capable of handling and controlling the automation process.”
FTI has launched Vision 2025, in order to try and lift the level of industrial development to 3.0 by the year 2020, and from 3.0 to 4.0 by 2025. It includes steps conductive to achieving Industry 4.0: 1) Raising awareness among all stakeholders so they can rethink about productivity, efficiency and cost. 2) Improving access to new technology, partly by talking to the, in Thailand not yet mature, banking sector concerning making it easier getting loans at reasonable conditions; and by trying to bring the cost of automation equipment down (reduced import duties on automation equipment). 3) Stimulate investment: “Right now in the manufacturing sector most if not all are already aware of the threat of not being productive and efficient, and of not being able to come up with a very high quality product. That is sometimes only achievable by automation, because the level of standardisation and precision of work that is required. Tax incentives and government policy is important in this regard. We are trying to make the Thai government come up with the policy to support this.” 4) Promote IoT: “Industry 4.0 has to be connected directly to the consumers, suppliers, and all other aspects of a business. We will try to promote so that all aspects of manufacturing can be connected seamlessly, and incur the minimum human intervention as possible.”
“We are going to try to do more with less but also, at the same time, doing the best,” Dr Chayo ended.
Among the company presentations Hexagon’s representative, Louis Mussa, said that essentially the technology for 4.0 is there today and accessible.
“The true key to be successful with it is to analyse the need of the customer and how the customer needs to be connected. Of everything out there you do not need everything to achieve your results. You may only need a very small part of it. And say if you have a line building cars, you don’t want to by another line; you want use the same things, redesign it, re-programme it to continue using it, and so on.”
Monitor ERP System’s representative Todd Abraham spoke about design principles of 4.0 inter-operability – taking digital and interfacing it with physical world to allow us to make faster core decisions.
“The question is how does a SME move itself along to try to keep up with development taking place in industries today. How can technology help digital and physical world come together and share info so that companies can respond faster to needs of customers, to also information transparency as a component,” Toddy describe the design principles of 4.0 inter-operability.
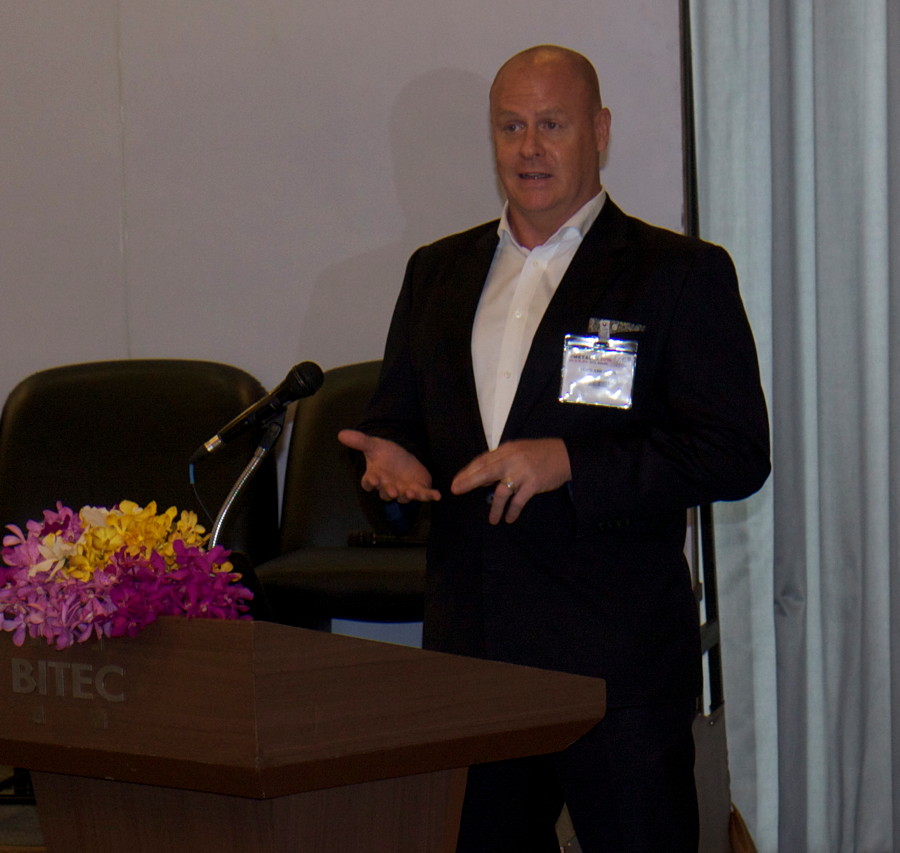
Todd Abraham, Monitor ERP System
“For SMEs looking at this new technology and how to make sense how to rein it, can be quite an overwhelming experience.”
He described it as somewhat of a big battle for a small business to compete and keep up, and make the investments. Todd recommended breaking it down into what is the current status of one’s business today: “What can we do to make operational, simple changes within our company so that those new operational efficiencies we can realise help add revenue to our bottom line. And hopefully by allowing new revenue that can help you to start making investments into new technology.”
“Of course, when you are making the operational changes it is helpful if you look at it from a systemic point of view, using a tool that can make sure you are collecting the data in a system that can help you continuously monitor and review your new state of excellence in your production department.”
Montor ERP offers a completely integrated system, enabling a systemic point of view in terms of data collection, monitoring and reviewing. Also, from an industry 4.0 perspective some tools are included that help to take a step along the way towards that bigger vision.
“We’ve been focused on manufacturing from the beginning, so you would be hard pressed to come up with a manufacturing company or scenario that we haven’t seen before. That means there’s very little requirement for any customisation to take place in order for our system to work, to meet your needs and the business processes you are working with today,” added Todd.
Pontus Rosengren from Virtual Manufacturing, with its new approaches to help leading manufacturers to reach operational excellence faster, presented their method for ‘surprise avoidance’.
One area of their expertise is where a client has a new factory or want to improve it, has a new line, or a new production cell.
“Surprise avoidance makes sure we know what’s going to happen and that we use as little energy as possible in saving your time and money.”
Virtual Manufacturing uses what is called digital factories for workplace visualisation.
“The value is that the team that will be working with you will have an understanding and will go in the same direction. We also think that you should make your mistakes in the digital factory rather than in the real.”
But everything starts in the real world: “You need to collect your data, and then you need to your factory performance KPI so you can show it to those working on the factory floor. From that data you can start doing simulations and from there optimisation. And from that you will get new KPIs and from that you start doing the changes in the real world again.”
That cycle is then repeated again and again.
Another is real time communication and visualisation, which is about being able to act in the right time, before the surprises occur.
Or human-machine collaborations: working with collaborative robots that can work and stand directly with people without safety fences.